How Can A Rotating Conveyor Be Used To Integrate Automation And Robotic Systems?
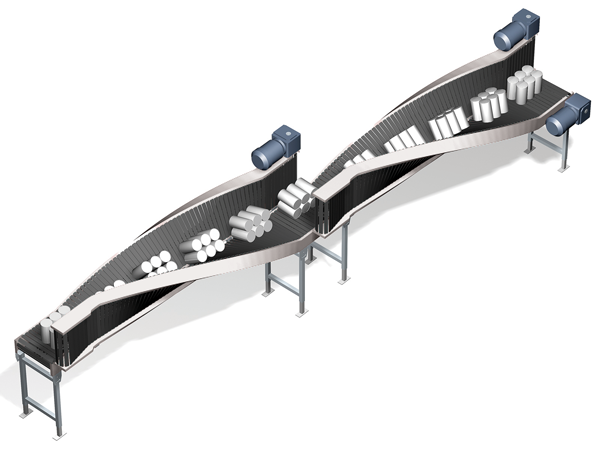
In today’s fast-paced manufacturing world, businesses constantly seek ways to improve efficiency and productivity. One key area of focus is the integration of automation and robotic systems into existing production lines. How can a rotating conveyor be used to integrate automation and robotic systems?
Rotating conveyors can integrate automation and robotic systems by providing a flexible, continuous workflow that allows robots to access multiple workstations or processing areas. This setup enhances efficiency, reduces downtime, and optimizes space utilization in manufacturing environments.
While this brief answer provides a good overview, diving deeper into the specific applications and benefits of using rotating conveyors in automated systems is important. Understanding these details can help you make informed decisions about implementing this technology in your production processes.
What Are The Specific Applications Of Rotating Conveyors In Automated Systems?
Rotating conveyors have numerous applications in automated systems across various industries. In assembly lines, they can move products between different robotic workstations, allowing each robot to perform its specific task as the item rotates past. This setup is particularly useful in electronics manufacturing, where multiple components must be added or inspected at different stages.
In the food and beverage industry, rotating conveyors can be integrated with packaging robots to create a continuous flow of products through filling, sealing, and labeling processes. The circular motion allows for a compact design that maximizes floor space while ensuring a smooth, uninterrupted production line.
Another application is in quality control and inspection systems. Rotating conveyors can present products to vision systems or other sensing technologies at various angles, enabling thorough automated inspection without complex robotic arm movements.
How Do Rotating Conveyors Enhance Efficiency In Robotic Systems?
Rotating conveyors significantly enhance efficiency in robotic systems through several key mechanisms. Firstly, they eliminate the need for robots to move between workstations, reducing wear and tear on robotic components and minimizing the risk of collisions or errors associated with robot movement.
Secondly, the continuous motion of rotating conveyors ensures a constant supply of work for the robots, reducing idle time and maximizing productivity. This is particularly beneficial in high-volume production environments where even small improvements in cycle time can lead to significant gains in overall output.
Additionally, rotating conveyors enable better synchronization between different robotic operations. By precisely controlling the rotation speed, manufacturers can ensure that each robot has the right amount of time to complete its task before the product moves to the next station, optimizing the entire production process.
What Considerations Should Be Made When Implementing Rotating Conveyors In Automated Systems?
When implementing rotating conveyors in automated systems, several important considerations must be made. First and foremost is the design of the conveyor itself. The rotating conveyor’s size, speed, and load capacity must be carefully matched to the specific requirements of the robotic system and the products being handled.
Another crucial factor is the integration of safety features. As rotating conveyors involve moving parts in close proximity to robotic systems, proper guarding, emergency stop systems, and sensor-based safety measures are essential to protect both human workers and the equipment itself.
Maintenance and accessibility are also key considerations. The design should allow easy access to the conveyor components and robotic systems for regular maintenance and repairs. This may involve incorporating removable sections or access panels into the conveyor design.
Lastly, the control system for the rotating conveyor must be carefully integrated with the overall automation system. This includes synchronizing the conveyor’s motion with the robotic operations, implementing error-handling procedures, and ensuring seamless communication between all automated system components.
How Can Rotating Conveyors Adapt To Different Product Sizes And Shapes?
One key advantage of rotating conveyors in automated systems is their ability to handle a variety of product sizes and shapes. This flexibility is achieved through several design features and technologies. Adjustable dividers or partitions can be incorporated into the conveyor system, allowing it to accommodate different product dimensions without requiring time-consuming changeovers.
Advanced sensing technologies, such as vision systems or weight sensors, can be integrated to detect the size and shape of incoming products. This information can then adjust the conveyor’s speed or positioning dynamically, ensuring optimal handling for each item. For example, larger products require slower rotation speeds or more space between items.
Furthermore, modular design principles can be applied to rotating conveyors, allowing for quick and easy reconfiguration of the system to handle different product lines. This adaptability is particularly valuable in industries with frequent product changes or seasonal variations in production requirements.
What Are The Future Trends For Rotating Conveyors In Automation And Robotics?
The future of rotating conveyors in automation and robotics is closely tied to broader trends in Industry 4.0 and smart manufacturing. One significant trend is the integration of IoT (Internet of Things) technologies into conveyor systems. This allows for real-time monitoring of conveyor performance, predictive maintenance, and data-driven production process optimization.
Another emerging trend is using AI and machine learning algorithms to enhance the capabilities of rotating conveyor systems. These technologies can optimize product flow, predict and prevent bottlenecks, and adapt the conveyor’s behavior based on changing production requirements or environmental conditions.
Sustainability is also becoming an increasingly important consideration in conveyor design. Future rotating conveyors will likely incorporate energy-efficient motors, regenerative braking systems, and sustainable materials to reduce their environmental impact while maintaining high performance.
Lastly, we can expect greater integration between rotating conveyors and collaborative robots (cobots). This combination could lead to more flexible and adaptable production systems, where humans and robots work seamlessly alongside each other, with the rotating conveyor serving as a dynamic, shared workspace.
Taking the Next Step in Automation
Now that you understand the potential of rotating conveyors in integrating automation and robotic systems, it’s time to assess your current production processes. Conduct a thorough analysis of your manufacturing line to identify areas where a rotating conveyor could enhance efficiency, reduce bottlenecks, or improve product handling. This evaluation will help you determine if implementing a rotating conveyor system is the right move for your specific automation needs and set you on the path to optimizing your production capabilities.